Choosing the Right Industrial CNC machining: Key Factors for Businesses
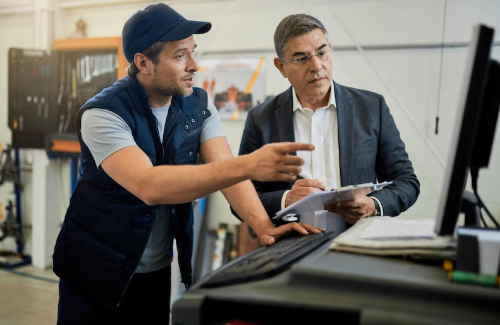
In today’s competitive manufacturing environment, choosing the right 5-axis CNC machine can be the difference between falling behind and leaping ahead. Whether you’re producing turbine blades, medical implants, or die-mold parts, the precision and flexibility of 5-axis machining go far beyond what traditional machines offer. As businesses shift from 3-axis to
Unlike legacy setups, a 5-axis machining center allows simultaneous movement along five different axes, reducing setups, increasing speed, and improving surface finish. This level of sophistication is no longer a luxury—it’s the industry standard for high-precision, high-value components. But with so many options and 5 axis CNC machine manufacturers offering similar specs, how do you decide what really matters?
This guide will walk you through the technical, strategic, and business factors that define the ideal fit. Because buying a 5 axis CNC milling machine isn’t just a capital investment—it’s a capability upgrade for your entire operation. This blog serves as a practical 5-axis CNC machine selection guide to help you make an informed investment.
1. Match the 5-Axis CNC Machine to Your Industry Application
Not all 5-axis machines are created equal, especially when you factor in application-specific demands. Whether you’re machining aerospace alloys or high-hardness steels for medical parts, choosing an industrial CNC machining that aligns with your industry’s tolerances and materials is step one. Choosing the best 5-axis CNC machine for business often depends on how well the machine handles the materials and tolerances specific to your industry. Aerospace demands lightweight yet strong materials like titanium, while the die-mold segment might lean toward hardened tool steels.
This is where precision, rigidity, software integration, and the right 5-axis machine capabilities come into play. While a 5 axis machining center might seem overkill for certain batch jobs, in sectors like energy, defense, or aviation, it’s a requirement—not an option. If your part tolerances are tight and repeatability is critical, don’t settle for a general-purpose model. Instead, explore 5 axis CNC machine manufacturers that offer custom configurations or upgrades for thermal stability, dynamic stiffness, and multi-material support.
2. Simultaneous vs. 3+2 Axis: Which One Fits Your Workflow?
A big decision when shifting to 5-axis is choosing between simultaneous 5-axis and 3+2 indexed machining. This section can serve as a helpful starting point in your 5-axis CNC machine selection guide, especially when weighing motion type against production needs. Simultaneous movement allows for continuous tool engagement across all five axes, ideal for intricate freeform surfaces like turbine blades. In contrast, 3+2 setups lock two axes in a fixed position while the other three move, making them suitable for less complex parts that still need multi-face access.
Simultaneous industrial CNC machining provides higher precision and better surface finishes but comes with a steeper learning curve and more complex programming. It’s essential to evaluate your part geometry, volume, operator skill level, and the specific 5-axis machine capabilities needed—before investing in the best 5-axis CNC machine for business. If you’re machining molds or sculpted surfaces, go for a 5 axis CNC milling machine that handles true simultaneous motion with ease. If you’re machining molds or sculpted surfaces, go for the best 5-axis CNC machine for business—like a Hermle setup—that handles true simultaneous motion with ease. For high-volume prismatic parts, a robust 3+2 setup might offer better returns.
3. Assess the Mechanical Structure of the 5-Axis CNC Machine
The mechanical foundation of a 5-axis CNC machine directly impacts its long-term accuracy and performance. From C-frame to gantry-style to trunnion-table designs, each layout offers different pros and cons. Trunnion tables offer better rigidity for heavy metal removal, while swivel heads provide greater flexibility in handling large parts.
If you’re unsure which to pick, revisit your part mix. A trunnion-table machine may outperform in vertical milling of die components, but if you work with long aerospace extrusions, you may need a gantry-based or swivel-head system. Also, keep an eye on 5 axis machining center specs like weight distribution, column rigidity, and damping features—all of which influence part accuracy over extended runs.
In such cases, the best 5-axis CNC machine for business is often a large-format gantry machining center that balances reach with rigidity. Also, keep an eye on 5 axis machining center specs like weight distribution, column rigidity, and damping features—all of which influence part accuracy over extended runs.
4Evaluate Spindle and Tooling Specs in 5-Axis CNC Machines
The spindle isn’t just a motor—it’s the heart of your machining center. You’ll want to consider torque, power, RPM range, and taper type when evaluating a 5 axis CNC machine. High-speed spindles (18,000–30,000 RPM) are great for aluminum and composites, while high-torque setups are essential for steel and titanium.
In such cases, the best 5-axis CNC machine for business is one that offers advanced spindle configurations suited for aerospace-grade alloys and demanding materials.
Also consider tool magazine size and changeover speed. If you’re operating a high-mix, low-volume shop, a larger automatic tool changer (ATC) can save you from constant reloading. Meanwhile, 5 axis CNC milling setups with built-in tool break detection or cooling-through spindles can minimize downtime. Always match spindle specs to your material and cutting strategies to maximize ROI.
5. Compatibility of the 5-Axis CNC Machine with CAM Software
No matter how powerful the machine, it won’t reach its full potential without compatible CAM software. A modern 5-axis CNC machine must integrate seamlessly with CAD/CAM platforms like Siemens NX, Fusion 360, or Mastercam. Look for post-processors that are tailored to your specific machine controller (Fanuc, Siemens, Heidenhain).
When you’re choosing a 5 axis CNC machine, don’t overlook the importance of ease-of-use in programming. Some machines offer intuitive UIs that shorten the learning curve for operators. Bonus points if your OEM provides post-processor optimization, simulation tools, or training modules. CAM-CNC synergy is the linchpin for cycle time reduction, accurate pathing, and surface finish consistency.
6. Understand Space, Power, and Cooling Requirements of 5-Axis CNC Machines
Before making a purchase, get practical about your space, infrastructure, and the 5-axis machine capabilities your facility can realistically support. A high-end 5-axis CNC machining center means nothing if it doesn’t fit your shop floor—or your power grid. Check the footprint, cooling system needs, and power consumption. Many 5 axis CNC machine manufacturers now offer compact models for smaller workshops without compromising on capability.
Also, be mindful of chip management and thermal stability. Machines with built-in coolant filtration systems and chip conveyors offer smoother operation. If you’re planning to machine tough materials like Inconel or hardened steel, go for a machine with enhanced coolant systems and thermal compensation to avoid heat-induced errors.
Factoring in infrastructure limitations is a crucial part of any 5-axis CNC machine selection guide, especially when floor space, power loads, and thermal demands come into play.
7. Calculate the Cost-Performance Ratio of 5-Axis CNC Machines
Price tags vary wildly—from ₹40 lakhs to ₹2 crores and beyond. But cost alone shouldn’t drive your decision to buy an industrial CNC machining . Instead, calculate a machine’s cost-performance ratio. Consider programming time, cycle reduction, tool wear, scrap rates, and rework frequency. A cheaper machine may look attractive but could bleed profits in the long run.
Often, the best 5-axis CNC machine for business is not the most expensive—but the one that consistently delivers ROI in high-precision, regulated industries like medical manufacturing.
If you’re testing waters, start with a refurbished 5 axis CNC machine that meets entry-level needs. As your production scales, migrate to high-end models with integrated automation and real-time diagnostics. Smart budgeting ensures you won’t overpay for unused features or underinvest in crucial performance benchmarks.
8. Support, Training, and Upgrade Options for 5-Axis CNC Machines
Even the most advanced 5 axis CNC machine is only as good as its support ecosystem. When shortlisting vendors, prioritize those who offer local service, remote diagnostics, and preventive maintenance contracts. Also check if the machine’s software and hardware are upgradable—so you’re not stuck with outdated tech after a few years.
Many 5 axis CNC machine manufacturers provide operator training, process consulting, and even CAM workshops as part of their onboarding. If your production includes automation or lights-out machining, explore how well the machine supports robot arms, pallet changers, or Industry 4.0 integration.
Invest in the Right 5-Axis CNC Machine with Long-Term Vision
Choosing a 5-axis CNC machine is not just a purchase—it’s a strategic upgrade that impacts everything from part quality and lead time to profitability and client satisfaction. As industries move toward precision-driven manufacturing, the demand for high-performance 5-axis machining centers will only intensify.
By focusing on the right combination of mechanical design, CAM compatibility, spindle performance, and vendor support, you can future-proof your shop floor. Whether you’re upgrading from a 3-axis or scaling your capacity, align your choice with both current production needs and future growth opportunities.
When in doubt, consult with experts who understand both the technical and business implications of CNC investments. Because in the world of manufacturing, precision isn’t a feature—it’s your edge.
Speak to a Phillips CNC machining expert today to get tailored advice for your business.